Users who have applied related products may understand that no matter what product is produced and used, its quality is the top priority, not only related to the use time of the product, but also related to the safety during production. Similarly, when purchasing high-pressure steel wire braided hoses that are too tight or have too few layers, the hoses will be deformed and susceptible to corrosion due to slight pressure, and the adhesion of the rubber layer and the steel wire layer will be insufficient. These conditions will make the tube wall prone to bursting.
First, let us look at the structure of the hose:
High pressure hose is generally composed of four parts: outer rubber layer, steel wire reinforcement layer, middle rubber layer and inner rubber layer.
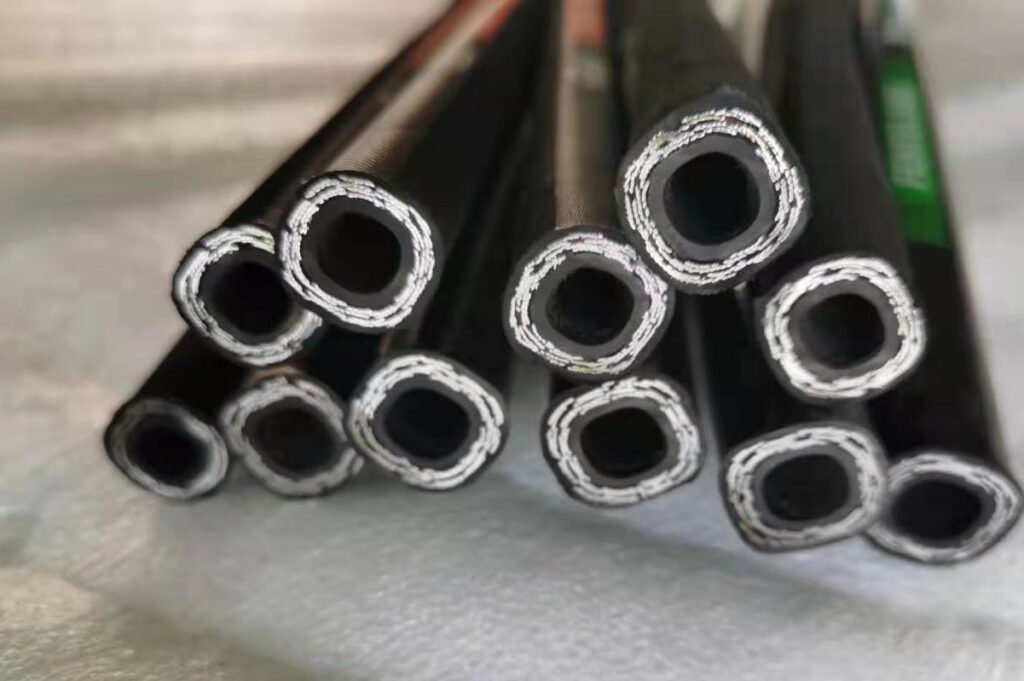
1) Inner rubber layer: Direct contact with hydraulic oil, generally made of black oil-resistant synthetic rubber, which has the function of making the conveying medium bear pressure and protecting the steel wire from corrosion.
2) Reinforcement layer: The bearing capacity of the hose depends on the reinforcement layer. This layer is the skeleton of the hose and is usually braided or wound by steel wires. For medium and high pressure, steel wire braids are mostly used as the skeleton, and steel wire wound skeletons are mostly used for high pressure and ultra-high pressure.
3) Outer rubber layer: generally made of black oil-resistant, corrosion-resistant, and abrasion-resistant synthetic rubber, with a textured surface to ensure that the reinforcement layer is free from mechanical damage, chemical corrosion, and moisture rust.
So how do we distinguish the quality of high-pressure hose? There are below points:
1. First look at the outer rubber of the high-pressure tubing to see if the surface is smooth and flat, whether there are bubbles, bumps, sponges, trachoma, etc.; when seizing, use a peeling machine to remove the rubber to see if the peeled rubber is continuous and continuous The ones are of good quality.
2. Look at the brightness of the cross section of the rubber tube from the outside. The high-brightness is the top grade, and the gel layer should be pinched with a nail to have good gel elasticity.
3. From the cross section of the hose to see whether the steel wire layer inside is uniform, it is distinguished from the diameter of the steel wire. The steel wire mesh of the hose is evenly distributed, and there is no missing part. The thicker the diameter of the inner steel wire, the better.
4. Look at the uniformity of the tube wall thickness of the inner rubber layer and the size of the inner hole of the rubber tube, and try to distinguish it with a standard joint.
5. Through the pressure test, the national standard requires the test pressure to be 2 times the working pressure, and the burst pressure is generally 3-4 times the working pressure to qualify.
6. Poor quality hoses will appear: the hose wall thickness is uneven; the steel wire braiding is too tight, too loose or the number of steel wires is too few; the deformation of the hose after pressure (elongation, shortening or bending) is large; Poor air-tightness of the rubber layer leads to corrosion of the steel wire; poor sealing of the inner rubber layer allows high-pressure oil to easily enter the steel wire layer; insufficient adhesion between the glue layer and the steel wire layer. The above conditions will reduce the bearing capacity of the hose, and eventually burst at the weak point of the tube wall.
To look at the material, you need professional knowledge and professional equipment to analyze. A simple method of judgment is to compare the weight of two pipes with the same diameter, wall thickness, and length. The calcium powder with the higher weight has too many impurities added, and the material is impure, which does not meet the requirements. Fire resistance is quite troublesome. The most direct way is to put it in a place with high temperature and high light for a few days to see the surface change rate.