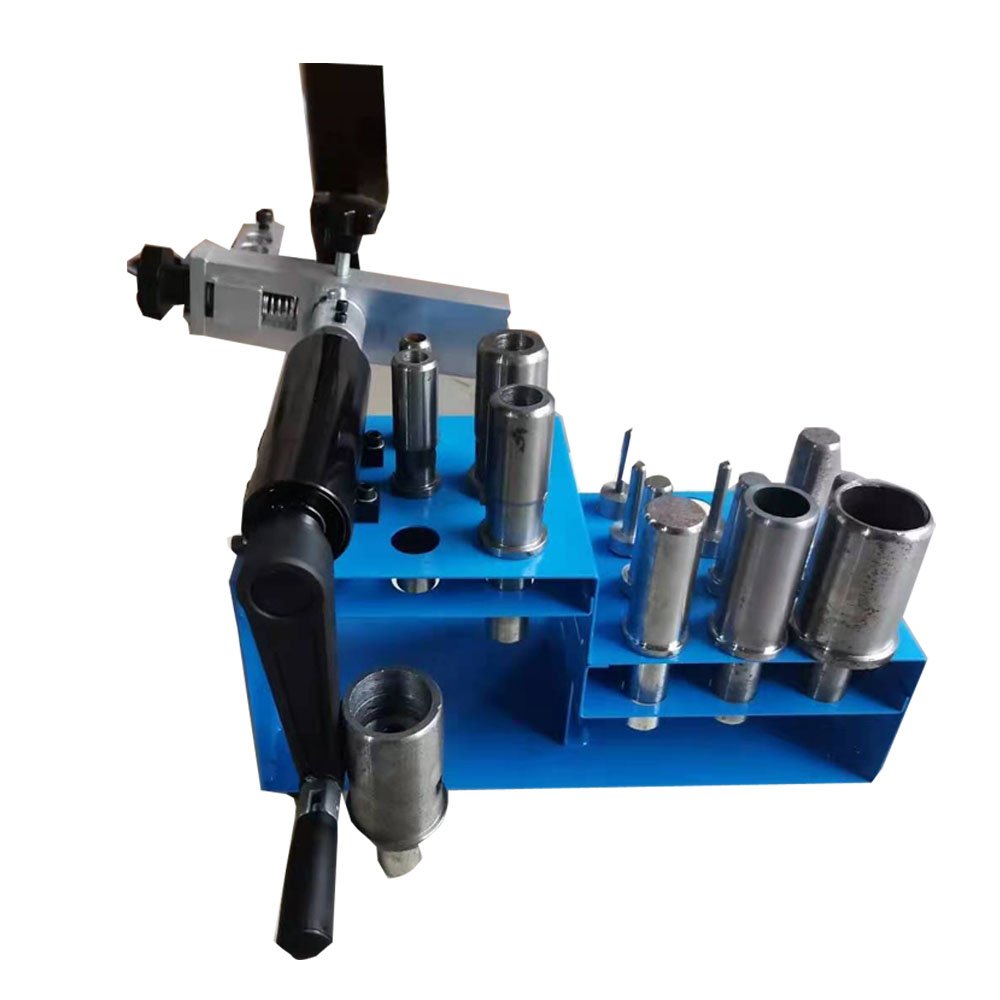
In the hydraulic hose assembly process, the manual hose stripping machine is a critical piece of equipment. Whether the stripping process is executed correctly directly affects the crimping quality, sealing performance, and service life of the hose assembly. Improper stripping length or depth can lead to hose leakage, fitting pull-off, or even hose burst accidents.
This article provides a comprehensive and practical guide to manual hose skiving machine operation. The article is structured as follows:
- Why Hose Stripping Matters – Explaining why accurate stripping is essential for hose safety and longevity.
- Key Parameters: Stripping Length and Stripping Depth – Detailing how to design the correct stripping length and control stripping depth.
- Step-by-Step Manual Operation Process – Offering a detailed, practical procedure suitable for on-site factory use.
- Practical Tips and Process Details – Sharing key techniques to improve stripping quality and operational efficiency.
- Common Mistakes and Risks – Summarizing frequent operational errors and potential hazards.
- Quality Control Checklist – Outlining the key inspection points after stripping.
- Advantages of Manual Stripping Machines – Briefly comparing manual and automatic stripping machines.
This structured content will help beginners quickly understand the stripping process and provide systematic quality improvement references for experienced technicians.
1. Why Hose Stripping is Crucial
Hose stripping is the process of removing the outer rubber layer of a hydraulic hose to fully expose the steel wire reinforcement, ensuring tight crimping with ferrules and fittings. Whether the stripping is done properly will directly impact:
- ✔️ The ability to securely crimp the hose without slipping
- ✔️ The reliability of the hydraulic system sealing
- ✔️ The service life and pressure resistance of the hose assembly
If the stripping length is insufficient, the crimping area will be inadequate, leading to leakage or pull-off. If the stripping length is too long, the exposed steel wire may rust or the ferrule may not fully cover it, creating serious safety issues.
Therefore, stripping length, depth, and cleanliness must strictly comply with technical standards.
2. Key Parameters: Stripping Length and Stripping Depth
2.1 Stripping Length Design
The stripping length must match:
- The hose size (inch specification)
- The fitting model and design
- The effective crimping length of the ferrule
✅ Correct Stripping Length = Crimping Length Specified in the Technical Drawing
⚙️ Note: Always follow the stripping length provided by your fitting supplier.
2.2 Stripping Depth Control
Standard requirements:
- Completely remove the outer rubber layer
- Fully expose the steel wire reinforcement
- No remaining rubber or semi-stripped surface
- No damage to the steel wire or inner rubber layer
Incorrect stripping depth consequences:
- Insufficient depth: Residual rubber impacts crimping, leading to leakage
- Over-stripping: Damaged steel wires, weakened hose structure
Correct stripping should leave the steel wire fully exposed, clean, and undamaged.
3. Step-by-Step Manual Hose Skiving Operation
Step 1: Preparation
- Confirm the hose model and fitting drawing
- Measure and mark the required stripping length
- Adjust the stripping machine blade depth and support position
- Prepare calipers, cleaning brushes, and other tools
Step 2: Set Stripping Parameters
- Select the correct blade opening for the hose size
- Adjust blade depth to ensure the rubber is cut without touching the steel wire
- Perform trial stripping on scrap hoses to confirm settings
Step 3: Perform Stripping
- Secure the hose in the machine clamp
- Rotate the handle steadily and maintain even speed
- Apply steady pressure without forcing the blade
- Ensure the rubber layer is fully removed during stripping
Step 4: Post-Stripping Inspection
- Measure stripping length accuracy (tolerance ±1mm)
- Check the steel wire condition (should be clean, no damage)
- Clean residual rubber from the steel wire layer
Step 5: Final Preparation
- If immediate crimping is not performed, apply anti-rust oil to the exposed steel wire
- Proceed to the crimping process
4. Practical Tips and Operational Details
- The stripping blade must remain sharp to avoid burrs or uneven edges
- Maintain a consistent stripping speed to ensure smooth surfaces
- Always test settings on scrap hoses before production
- Clean residual rubber and debris with a small brush after stripping
- Ensure the clamp holds the hose firmly to prevent slipping during operation
5. Common Mistakes and Potential Risks
Mistake | Potential Risk |
---|---|
Stripping length too short | Inadequate crimping area, risk of pull-off |
Stripping length too long | Ferrule may not fully cover, leakage risk |
Insufficient stripping depth | Residual rubber, poor sealing |
Over-stripping, steel wire damage | Reduced pressure resistance, hose failure |
Inconsistent stripping speed | Uneven surface, difficult to clean |
Ignoring technical drawings | Assembly dimension mismatch |
6. Quality Control Checklist
Inspection Item | Requirement |
---|---|
Stripping length accuracy | Tolerance ±1mm, must match drawing |
Steel wire condition | No cuts, no broken strands |
Surface cleanliness | No remaining rubber, no burrs |
Hose roundness | No significant deformation |
Cleanliness | No dust, oil, or rubber debris |
7. Advantages of Manual Hose Stripping Machines
Benefits
- Low investment cost, ideal for small batch production
- Easy to operate and maintain
- Highly flexible for emergency repairs and on-site assembly
- Adaptable to non-standard stripping lengths and special requirements
Limitations
- Lower efficiency compared to automatic machines for mass production
- Requires higher operator skill and attention
Manual stripping machines are especially suitable for repair shops, small factories, or companies with frequent specification changes and low production volumes.
8. Conclusion
Although manual hose stripping machines are simple in structure, the precision of the stripping process directly impacts the safety and reliability of hydraulic hose assemblies. Proper stripping length design, accurate stripping depth control, and strict adherence to operating procedures are critical to maintaining product quality.
✅ Key Takeaways:
- Always follow the stripping specifications provided by the fitting manufacturer
- Stripping length and depth must be precise, never adjusted based on guesswork
- Inspect the steel wire and residual rubber carefully after stripping
- Maintain the stripping machine regularly to ensure blade sharpness and stability
By following standardized procedures and strict quality control, manual stripping can be a safe, efficient, and cost-effective step in your hydraulic hose assembly process.